On behalf of Erol, Michael and everyone at MiniFAB, have a joyful festive season, a happy new year and a successful 2013. We look forward to working with you in the coming year.
CEO Report
Productivity is a buzz-word we are hearing more frequently. Your view on the question "how to get more from existing resources?" frequently depends on the context of the discussion. Public funders of R&D ask what impact their spending has had and quickly follow with questions about effective paths for translational research and best practice in commercialisation. Health funding agencies are acutely aware that their current funding models cannot keep up with increasing demand within an ageing population. Emerging technologies hold promise to improve health outcomes, however increasing costs and increasing expectations for equitable access to the technology will stretch existing resources. And innovative companies need to build and constantly adapt their business models to increase productivity and maintain their competitive edge.
We live in an increasingly connected world, so unsurprisingly there is a strong connection between these three productivity scenarios. Another phrase I have heard used more frequently this year is the "innovation ecosystem" - a good term for understanding the interconnections and the roles each business play. Productivity is often not something you can improve on your own. It invariably involves working with others and depends upon how well you are connected to the skills and resources you need. The health of the innovation ecosystem depends critically on the strength of businesses that act as connectors, and MiniFAB is one of these. One of our clients recently called us a "contract manufacturer on steroids". I think he was referring to the connections we make in bringing new products to market.
This has been an interesting year in which we have participated in moving some exciting technologies out of universities into markets. A talk I gave at the San Diego LOAC World Congress on "5 Tips for Commercialising Lab-on-a-Chip" generated quite a bit of interaction. The innovation ecosystem for microfluidics and lab-on-a-chip is not regionally focused, it is global. MiniFAB develops and manufactures diagnostic devices for partners and markets around the world, and we use the skills and expertise of smart people no matter where they live. Point-of-care diagnostics with integrated sample handling are now a reality, but the rebate and funding models for health care are not keeping up with the emphasis change from treating sickness to ensuring wellness.
As a global community it seems to me that this is the next challenge for us to address. It is not technical because most of the technology is now available. It is about money and how to get the most out of it. It is also about productivity improvement and connectivity. As with any challenge it brings great opportunities for new approaches and the business success that comes with it. But most importantly, getting this right will change people’s lives. That seems to me worth doing.
Erol Harvey - CEO
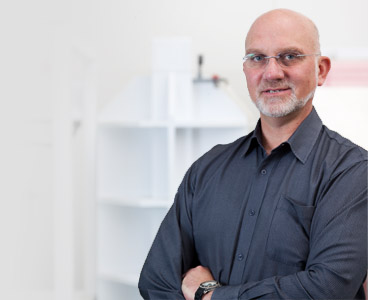
Celebrating 10 years of MiniFAB
This week MiniFAB is celebrating 10 years of developing and manufacturing polymer micro-engineered products.
To commemorate the occasion, we spoke with MiniFAB's team about the company's past, present and future. Put faces to MiniFAB's names and explore the MiniFAB environment in these three short videos.
"10 years of MiniFAB history has been quite an achievement, it's really built up to the point now where we are considered world experts in our field, developing engineered solutions for our clients," said Andrew Campitelli, Business Development Manager.
With a team of over 60, 900+ completed projects, approximately 1,500,000 parts produced and satellite offices in the US and Europe, in addition to the 4,000m2 facility in Melbourne, Australia, the company has come a long way from the small group that spun-out of Swinburne University of Technology in 2002.
"We've grown in two different areas, the development group has become a lot more specialised in what they do, and the manufacturing side is now bigger than the development side, which is great to see," said Jason Hayes, one of the first engineers to join the company and Product Development Manager.
"When we started 10 years ago, the understanding of lab-on-a-chip devices was pretty poor, we spent a lot of time educating clients on the platform. These days we're seeing clients come to us with much more developed projects. There's a better understanding of microfluidics in the industry at large," said MiniFAB CEO, Erol Harvey.
With many successes under their belt, like moving the award-winning TearLabTM Osmolarity Test Card from a concept to scaled-up manufacturing in under two years, MiniFAB is looking toward the future of precision engineering.
"We're lucky to live in a really exciting century where biology, medicine and engineering are coming together in a way that's never happened before. Things like our bionic eye project where we're aiming to bring vision to people who are visually impaired," said Erol. MiniFAB is part of the Monash Vision Group, which is working towards delivering a cutting-edge bionic eye implant ready for clinical trials in 2014.
"MiniFAB has grown and changed constantly, and it's always been fun. We've maintained that family feel, we're all good friends and enjoy working with each other, and also with our clients as well, they're part of our community too," said Dr Matthew Solomon, another project engineer who's been with the company from its Swinburne days.
"We're celebrating 10 years by having a party, which is the best way to celebrate 10 years, looking back on what we've done, learning from that and really looking forward to an exciting next 10 years," said Michael Wilkinson, MiniFAB's Executive Chairman.
"We're looking forward and we're trying to see what the next five years and the next ten years will be, every scenario we look at is exciting, great opportunities for us," said Dr Jason Hayes, Manager of Product Development.
To hear more from MiniFAB's staff about 10 years of product development and manufacturing, see these short videos.
Where we'll be

Join MiniFAB at the SLAS annual conference in Orlando, Florida from the 12th – 16th of January 2013, Booth #426
Start the New Year by connecting with MiniFAB at the Society for Laboratory Automation and Screening's Annual Conference in Orlando, Florida.
January 12 – 16 next year MiniFAB's Andrew Campitelli and Laura Faulconer will be at Booth #426 engaging with visitors about MiniFAB's specialised suite of services that rapidly translates concepts into fully manufactured microfluidic solutions for diagnostics and medical devices.
"We're looking forward to meeting with the SLAS community and sharing our expertise in product development and manufacturing," said Andrew.
Andrew will be presenting a poster on 'Blister techniques for On-Cartridge Reagent Storage'.
The team are also looking forward to hearing some of the conference's keynote speakers, particularly Dr Mehmet Toner's presentation on 'Bioengineering and Clinical Applications of the Circulating Tumor Cell Microchip'.
To arrange to meet with Andrew or Laura at SLAS or outside the show, please email andrewcampitelli@minifab.com.au

Also find us at Molecular Med TRI-CON 2013 in San Francisco, California from the 11th-15th of February 2013, Booth #221
Email andrewcampitelli@minifab.com.au to organize a meeting at the event
Strong Bonds

You've spent time, resources and a lot of effort developing your complex microfluidic device, but have you considered how you're going to seal it? Bonding: it's an absolutely critical part to any microfluidic cartridge, but one that doesn't get much airtime.
Choosing the best method for enclosing microfluidic channels or adhering two cartridge portions together, of course it's not as simple as a single 'best' option, hence the importance of having alternative strategies and the technical know-how to determine the best approach.
Rather than being limited to a single bonding capability, MiniFAB has a suite of materials and processes, including thermal lamination, solvent assisted bonding, pressure sensitive adhesives, laser welding, and more, that can be used to rapidly test bonding of disposable cartridge components.
"Having multiple options for bonding is vital to the success of a project. Each cartridge has its own unique set of specifications that will influence the choice of bonding format; PSA, thermal, solvent... each has advantages and disadvantages, it's about choosing the one that matches the cartridge," explained Peter Münster, one of MiniFAB's highly skilled Project Managers.
Central to decisions of bonding formats are considerations of material compatibility as well as biocompatibility of the process. For example, if a reagent is temperature sensitive a thermal assisted bond may not be the best solution. Other considerations in selecting a bonding process include the material costs and feasibility of using the selected process in a high-volume manufacturing environment.
"It's about having the know-how to recognise what process will work, as well as he capability to implement each," said Peter.
MiniFAB's bonding capabilities are constantly growing as clients come to us with new and challenging specifications, such as one past project where the bond was required to withstand pressures of 70-100psi. In another notable project MiniFAB was able to consistently achieve a clean bond on channels just 5-10 microns deep.
Choosing the right bond option is critical during the early phases of a development program and can be the deciding factor in the delivery of a strong, repeatable and reliable microfluidic cartridge or product.
Partner News

MiniFAB and Tearlab Corporation have celebrated the delivery of the 1,000,000th TearLab™ Osmolarity Test Card earlier this year.
TearLAB's Vice-President of Manufacturing and Engineering, Steve Zmina, presented the MiniFAB Production team with a plaque of achievement while in Melbourne in November.
"Whether MiniFAB were making single cards by hand or manufacturing hundreds of thousands of cards, they never compromised on the quality," said Steve.
Steve added that MiniFAB manufacture the TCI cards repeatedly to sub-micron tolerances, using a process that is scalable to meet TearLab's exponential growth.
At the presentation Steve spoke about how MiniFAB and TearLab have grown the product together from a concept in 2006, to prototypes, through small volume production and manufacturing ramp-up, to today where an automated manufacturing process produces over a hundred-thousand cards per month.
Michael Wilkinson, MiniFAB's Chairman, highlighted the importance of the strong relationship between the two companies and how that has been critical to the success of the product. "I remember back in 2006 leaving the office at 3am and receiving a phone call from our development team and TearLab's CSO Ben Sullivan who were all still in the labs; 'It's working!' they said. It's that sort of ongoing commitment and collaboration that sees this product and our companies continue to grow," said Michael.
What's New MiniFAB's New Website

MiniFAB launched its revamped website at www.minifab.com.au in September. Safe to say we're pretty chuffed with it.
This user- and mobile-friendly site provides comprehensive details about our flexible and open engagement model, the product development process, and our services that convert early-stage product concepts into prototypes and on to OEM volume manufacturing, all within an ISO 13485 environment.
The new site will enhance each visitor's experience, providing valuable information about MiniFAB's services, a portfolio of completed projects, and a FAQ section to address questions commonly asked by those undertaking custom microfluidic product development.
"The microfluidic world is rapidly developing and our clients are becoming more sophisticated and better informed about their needs. Our new site responds to this change, while at the same time maintaining its approachability and staying user-friendly for newcomers," says MiniFAB CEO, Erol Harvey.
Although MiniFAB is making changes to their online presence, our goal remains the same: to create business success for our partners by developing and manufacturing real world solutions and products using advanced micro-, nano-, and bio-engineering.
For regular news and updates from MiniFAB, take a look at MiniFAB on Facebook or join MiniFAB on LinkedIn.